Polished Concrete & Terrazzo
Polished Concrete and Terrazzo floors are one of the most popular types of flooring today. You can transform old or current concrete slabs with the most versatile, and durable flooring surfaces on the market, all while capturing the elegance of polished marble or granite. 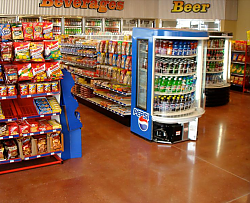
Another obvious but often overlooked aspect of polished concrete and Terrazzo flooring is that fact that you are utilizing the existing substrate. All other flooring goes on top of a substrate of some kind, and at some point will peel, flake, stain, chip, bubble, or fade. Stop the wax and strip cycle forever and save Thousands over time.
What is the Process of Polishing Concrete or Terrazzo?
Concrete or Terrazzo Polishing is a multi-step process, first using course diamond impregnated metallic disc that helps remove light coatings, blemishes, and small pits from the surface. Depending on the current state of the floor, the metal bonded disc very in grit from 16-300 grit. A number of metallic discs may be progressively used to a finer grit to achieve the proper surface to be polished. Once the initial cut is complete, a similar process using resin bonded pads is started. The first pass with resin pads is 100 Grit and goes all the way up to 3000 Grit. The finishing Grit is determined by the desired look by the client.
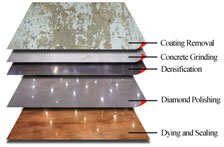
Click here to enlarge image.
Step 1: Prep
Clean concrete/Terrazzo slab to remove paint, oil spots, dirt, neural ph detergent and rinse. Repair/fill any surface cracks.
Step 2: Grinding
Multiple passes are made with various Metal Bond Diamonds to bring the concrete/Terrazzo to a uniform finish.
Step 3: Densification
A densifier is added during the process to increase the abrasion resistance of the floor and to eliminate dusting on concrete.
Step 4: Polishing
Multiple passes of Resin Bond Diamonds are used to polish the floor to the customer’s required level of gloss. A concrete floor is considered polished after the 800 Grit Resin Diamonds. You can take the polishing all the way to 3000 Grit Resin.
Step 5: Dying
Penetrating dyes can be added during the polishing steps to give concrete a particular color. Multiple colors and saw cuts can be used to create unique designs.
Step 6: Sealing
A penetrating sealer is not necessary but can be added to protect from highly acidic, or harsh chemicals that can stain or etch concrete.
Step 7: Burnishing
Burnishing the floor with a ”hogs hair” pad will bring out its natural shine.
Step 8: Job Site Cleanup
Click here to enlarge image.
Polished Concrete and Terrazzo are the Real "Green Solution"
As rigorous standards of sustainability continue to rise and the construction industry's quest for environmental-responsibility continues, finding affordable, sustainable building products will become a necessity for new construction, additions, renovations and remodels. Natural, durable and beautiful polished concrete and Terrazzo flooring is sure to become a widely-used application, and though it may be wrapped in a gray package, polished concrete and Terrazzo flooring is an intrinsically green solution! Here's why:

Dematerialize the Project
Concrete is a fundamental part of every construction project - whether new construction or a remodel. Adding any extra material to a project results in greater expenditures and environmental stressors such as harvesting, manufacturing, refining and transporting another product to the job site. Finishing the floor by simply polishing the existing concrete material avoids these stressors while substantially decreasing the environmental footprint of the project, and saves on everything from natural resources to the pollution and costs associated with shipping.
Reduce Airborne Contaminants and VOCs
Up to 30% of the population have chemical sensitivities. Stemming from the “sick building syndrome” of the 1970s, indoor air quality is one focus of green construction. Polished concrete contributes no noticeable VOCs in the construction process, improving the indoor air quality.
Optimize Energy Efficiency
The reflective nature of polished concrete and Terrazzo reduces the amount of artificial illumination needed by maximizing the natural and artificial lighting already in use, thus improving energy efficiency of the lighting system as a whole.
The thermal mass gained from constructing with concrete, including walls and exposed concrete floors, in conjunction with passive solar design principals, moderates the daily temperature fluctuations, reducing the load on HVAC systems.
Concrete Polishing FAQS
(click on the title for the answers)
Why Choose DPDG ?
Our competitors will try to sell you a “polished” concrete system for full price while providing you nothing more than a chemically densified and burnished concrete slab using a high speed buffer. This option will look great for the first six months and slowly revert back to bare unpolished concrete. Just look at your local Lowes or Home Depot and then take a look at your granite countertop at home; that’s the difference. DPDG strictly adheres to the Concrete Polishing Association guidelines for surface cut and reflective clarity.
Why would I polish concrete or Terrazzo instead of coat it with a high quality sealer or epoxy?
Depending on the specific uses of a floor, coatings may be a better finish in the long-run. Polished concrete is a treatment to make the concrete surface more abrasion and stain resistant. However, it should never be confused with a coating in that it is still prone to staining and etching if exposed to oil or acids; even mild acids like soda or orange juice will etch polished concrete. Polished concrete can be used on projects that need to withstand foot and/or wheeled traffic, will be washed regularly, not intended to resist stains and not intended to handle acid attack. If the preceding criteria are met, then a polished concrete surface is the perfect choice for long term durability and beauty. Typical applications include airplane hangars, schools, manufacturing businesses, distribution warehouses, parking structures, retail locations, airports, convention halls and residential slabs.
How often does a polished concrete or Terrazzo surface need to be washed?
Typically once a week is all that is required to maintain a polished concrete slab. An auto scrubber works best for this, but smaller areas can be done with a mop and wet vac. For cleaning solutions/products, there are none. The owner only has to use water to maintain a polished concrete surface.
What is the long term benefit of polished concrete and Terrazzo?
Polished concrete and Terrazzo are the most durable flooring system when compared with typical flooring finishes. It requires very little maintenance which basically amounts to weekly washings with an auto scrubber and water. When compared to other flooring finishes, their respective maintenance schedules and serviceable life spans polished concrete is the cheapest flooring system to own. Another benefit of polished concrete and Terrazzo is that the maintenance of the floor will not harm the environment with harsh chemical or wax residues. Since the floors only need to be washed with water, the waste can go directly into a sanitary drain without any soap or chemical residuals.
For instance, VCT (vinyl composition tile) requires regular waxing, buffing and stripping to keep it looking good. The cost of labor combined with chemicals usually costs the owner an average of $1 per square foot/per year. Then after 10 years, the floor starts to show it's age and needs to be replaced. This cost could easily be double the original installation cost. Concrete and Terrazzo polishing requires only auto scrubbing weekly; forever. The same is true of epoxies and carpeting; regular, costly maintenance with a relatively short life-cycle when compared to polished concrete or Terrazzo.
What makes polished concrete and Terrazzo so durable?
The polishing process by itself does very little to contribute to the longevity of the flooring finish unless a densifier is used. A densifier is a chemically reactive product that reacts with compounds present in all concrete slabs. The densifier is typically a Silicate solution that is carried by Lithium, Potassium or Sodium and applied by sprayer or broom during the polishing process. The chemistry of the reaction that takes place is detailed, but the most important fact to note is that the chemical reaction creates a 'skin' of sorts on the concrete that is very abrasion resistant and is the sole reason a polished slab retains its shine.
Is polished concrete expensive?
The initial procedure of polishing concrete is typically greater than conventional flooring finishes. To provide a polished concrete floor, contractors must own expensive and specialized pieces of equipment. This combined with the vast experience a qualified contractor should have makes the owning and operating of a polishing business very expensive. However, when judging whether to own a polished concrete floor, an owner/architect needs to gauge the cost of the flooring over the building's life span and the day-to-day operating costs that are incurred for regular maintenance. In almost all cases, polished concrete is the cheapest floor to own.
Can a polished concrete slab be colored?
Polished concrete can be colored using dyes or new slabs can be poured with integral color and then polished. The results of each process is very different in final appearance, but it is important to note that concrete can be dyed or poured in a wide variety of colors to match any color scheme. Another popular way of customizing polished concrete is to add decorative aggregates to fresh concrete. Contractors regularly use marble or granite chips, colored glass and natural shell to provide a completely unique floor that has a place in the highest end offices and homes.
How do I know if my concrete can be polished?
In most cases you don't. The only way to know if your concrete is able to be polished is to perform a mock-up or sample. This sample should be done on all slabs, new or old, so the owner is aware of the final product as well as providing the contractor with the proper procedure to achieve the desired finish. The good news though is that new and old slabs are polished every day, regardless of age and in our experience we have had only two slabs in five years that didn't polish.
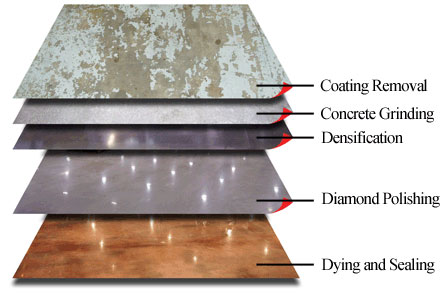